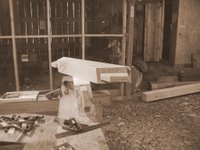
In the timber framing workshop at Grand Oaks, Scott tried to let us cut as many different types of timber framing pieces as possible. On the third day of the workshop, I was to cut some braces for the cabin frame. It took me an entire day to cut only two braces. In the back of my mind, I was thinking about how many braces would be in the house I wanted to build... 130 braces, divided by two per day = 65 days just to cut the braces for my house! Of course I would get faster as time went on, and surely I could employ some shortcuts, but my wife was also adament that our braces have those arches in them "like the ones in the magazines!" That would surely add time to the estimate. In any case, this would be repetitive work and would take a long time.
In my workshop at home, I had an old Super Max milling machine... a Taiwanese knock-off of the classic Bridgeport milling machine. It was retrofitted with a circa 1984 CNC system that I had never used for anything other than a digital readout. (and gee whiz, you could even save your programs on this machine if you had a cord to connect it to a cassette recorder). The machine was a free worn out hand-me-down from a company that wanted to get rid of it several years before. (you can buy a machine like it on ebay for probably $1,500) The gears were turning in my head... could I possibly program this machine to cut braces for my timberframe house?
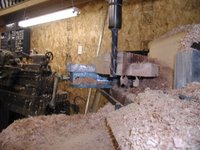
I did some experiments on little pieces of wood, and the short answer was a definite "maybe." The x-y travel was not large enough to do the entire braces at once - I would need to clamp the brace 3 different times (once for each of the 2 tenons and once for the arch), and I would need to find some very long 1" endmills. So for a few weeks I monitored ebay, and surely dried up the world's supply of surplus 1" endmill that were at least 4" long, snatching them whenever I could for roughly $10 apiece. (it eventually took about a dozen of them for my house)
The first time I fired up the machine and started the program I had entered on its keypad, the ol' Super-Max squealed, vibrated, screamed, and shuddered as it drove the 1" endmill trough the wood. The bit got duller and duller as the program executed. Eventually, smoke was rolling from what was minutes before a shiny new endmill. I manually overrode the feed rate, so that now the program was executing at about 1/10th of its intended speed. My spirits sank as I backed away from the howling machine, certain that something would break, but determined to see this first try all the way to its end. The very last step of the program was a command to drill (vertically) a hole for the peg in the end of the brace. Lo and behold, the machine executed this last step as if it were milling butter. Eureaka! We're back in business baby.

The key to making the milling machine work was not to mill a path sideways through the wood, but instead to approximate the shape I was trying to obtain by executing a series of vertical drilling operations... then and only then mill sideways, cleaning up the small bumps that resulted from the drilling operations. Connect the dots if you will. Ironically, this is how the old timberframers made their mortises (and how we were taught in the class) - they would drill into the wood, and then use a chisel to form their approimation of a mortise into a nice square mortise.

I made over 130 braces this way on my milling machine. Each brace required 3 programs, and each program took about 15 minutes. That's about 10 days of milling - I estimate this machine saved me about a month of repetitive work. What's more, when the program was running on the milling machine, I was able to surf the internet 15 minutes at a time, looking for more information on timberframing! Where precision matters the most in a timberframe (the braces), I was able to achieve a very high degree of precision.

When the CNC mill finished the very first brace, I slapped some Minwax polyurethane on it and ran to the house to show my wife. Here it is, still wet.
0 Comments:
Post a Comment
<< Home