
Still on the hunt for more hardwood flooring, or a millwork company able to mill our own boards into flooring, my wife and I scheduled a visit to a local flooring factory. With a throughput of 50,000 square feet of flooring per shift, and 99.99% of sales to commercial clients, we didn't think this company would be able to make us any bargains, or much less, be willing to mess with milling our boards. But they were local, so it was worth a shot.
We were pleasantly surprised to walk into the deal of a lifetime. In a dark corner of their factory were several stacks of over-runs from custom orders for big clients. The factory just wanted these "little" stacks out of their way. To make a long story short, we were able to buy assorted ash, hickory, cherry, walnut, and quartersawn white oak for cheaper than the yellow poplar flooring I had found a few weeks befo

re. In fact, the price was even cheaper than anyone would charge to mill my boards! Ash and hickory in strips 2 1/4" wide (and variously stamped "select and btr.", "no. 1", and "rift & qtr") made up the bulk of what I brought home. From what I've gleened from the internet, this is perfect flooring for placing over radiant heat floors. Narrow boards mean more boards per square feet, which means more joints to spread out the seasonal expansion and contraction in the boards (radiant heating can exacerbate this seasonal variance). The narrow strips are also less likely to cup I suppose. Finally, the quartersawn boards will have less expansion and contraction than plain sawn boards. Score!
I wasn't able to sort through (or even really look at) the flooring before I agreed to buy it, but I did notice from looking at the ends of the pallets that the 2 1/4", 3" and 5" wide cherry boards had no bevel, whereas the 4" cherry boards did have a bevel. No problem - all of the 4" cherry boards will go in one room by themselves.
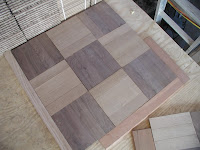
The walnut and white oak boards are milled for a herringbone style installation (they all measure 3"x12" with t&g on the ends). This will slow down installation, but make for some really neat floors. In fact, we're thinking of doing a checkerboard pattern in one of our son's rooms, by installing the boards parquet style instead of herringbone style and alternating between white oak and walnut. He's taken a keen interest in chess, and could even play a game on the floor... if he keeps it clean.
The only downside to all of this flooring (as opposed to the long 6" poplar boards or oak and ash boards that I would have milled from my own wood) is that it is not suited for nailing directly to floor joists. My scheme of building a house without plywood subfloor has now evaporated. The plan has morphed, so that now the entire house will have a subfloor and we have been busy as beavers installing subfloor everywhere (except where we already installed poplar, sans subfloor), and the house is now a much friendlier place to work.

While I'm on the topic of subfloor... Much of my house has rough-sawn oak 3x3's for floor joists (running perpendicular to the sparsely space 6x8 timber floor joists). The problem (or trick) of using saw-mill lumber is to develop methods of dealing with the variations in thickness, as none of it has seen a thickness planer or kiln before being placed into the structure. First of all, I started at the sawmill by cutting 3x3's instead of 2x4's. That way, I have 2 chances to get the critical 3" height of the board correct at the saw mill. When we install the 3x3's, if we find a 3x3 that measures 2 3/4" by 3", we place the material so the 2 3/4" dimension does not matter. It's also important to make sure the 3x3 spans at least three timber floor joists, so that when it dries it will not bow up or down. And finally, when you go to install flooring above the 3x3's, you can shim the short ones (2 7/8"?) up with strips of roofing felt. That's an idea that I came across somewhere on the internet and I can report that it works very well. You can see subfloor glue, as well as some of these black shim strips in this last picture.
Almost forgot to mention... those are drywall strips (cutoffs and waste) that we're using to hold down the radiant tube until the floor goes down. After the floors are installed, we'll pull out the drywall strips and tack the radiant tubing up from below. My brother-in-law gets credit for the drywall trick (careful, I have more than one bro-in-law that I talk about in these blogs... one person just couldn't be that smart or helpful.)
2 Comments:
Hey, Thomas!! You and Rhonda have a beautiful home!! I have been keeping up with your blogs and I have to say..you are doing one heck of a job!!Just from your pics, I can see the two of you will have one beautiful home. All your hard work will be something you and your family will cherish for many decades to come!! Best wishes!!!
Thomas,
I tried to reach you last night but the phone was busy. Is the weather now forcing you to come to stop or is the house now in such a condition that you are not effected by the weather? Things look like they are going great and the level of design (read "MIT over engineering") is truly amazing to me. I did not know what I was missing when we built our Squam house. -- Bill
Post a Comment
<< Home