
A "cricket" is the word used to describe a roofing feature whose purpose is to divert water where two roofing planes intersect. I needed a cricket where the tower roof intersects the main roof. Technically, the cricket was already built of lumber and covered with felt paper. What I needed to build now was the flashing for the cricket. I chose stainless steel flashing, because this would be one of the most difficult areas to "reflash," should the flashing ever wear out. Copper flashing would have been easier to fabricate, but could have worn out in 50 to 75 years. I'm hoping the stainless will last much longer. Yeah, yeah, I know I'll be dead by then, but I wouldn't want to burden the next owner with this onerous task (one of my kids?).
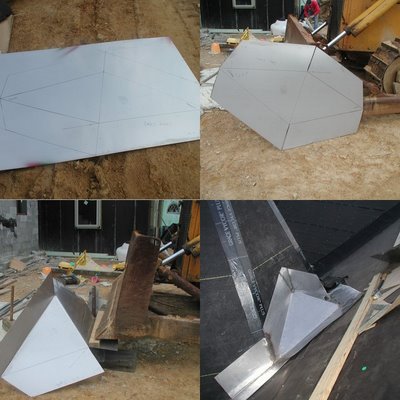
I cut the pattern from a sheet of 18 gauge stainless steel (anything thinner is almost impossible to MIG weld with my Lincoln) using a Stihl chop saw with an abrasive cutting disk. My bro-in-law helped me brake (sheetmetal term for "bend" or "crease") the angles using a bulldozer blade to clamp the stainless between two straight pieces of wood. I shoved on the steel, and he convinced it to fold using a hammer. Much to our surprise, the whole shebang started looking like an F-117 very quickly! I went over one of my welds with solder to make sure any pinholes would be sealed, but this was a real pain in the butt, because the weld spatter and gas had really contaminated the stainless. After that little detour, I decided to just go over all of my welds a second time with the MIG and call it "good."
It took two days for me to fabricate this thing (which included wrestling this monster on and off the roof for test fitting a few times). Like I said, copper would have been easier. The bottom right picture in the photo-collage shows the final piece in place on the roof. Helicopter passengers notwithstanding, no one will really ever see this detail on my house. I've also got to think... perhaps someone who does this for a living is going to read this and laugh his butt off when he sees how I made my cricket. As long as it works... forever... I don't care. :)
1 Comments:
obviously spam, but it's an ironic reminder that I'm using an even more obscure meaning of "cricket", so I think I'll leave it. Play on!
Post a Comment
<< Home