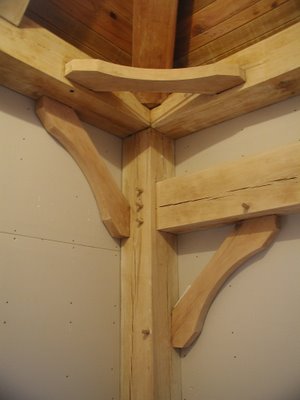
With the weather outside turning nasty, and the roof almost finished, we've turned out attention to hanging the drywall on the inside of the house. Like everything else, this is turning out to be a bigger job than I had imagined. The biggest time sink is cleaning (with bleach and/or sand paper) all of the weathered timbers inside the house. I'm not bothering to oil or finish the timbers at this point, because the mud-tape-sanding of the drywall is going to generate a lot of dust that could stick to the linseed oil. When we're completely done with the drywall, we'll go back and oil the timbers (hopefully one last time!).
The timberframe has never looked as good as the day it was standing naked against the blue sky. In fact, it kind of disappeared in the details of the rest of the house. But with each sheet of drywall that we hang, the timbers "re-emerge" more and more from the background of SIPs and studs. So with the exception of the laborious sanding, this is a very exciting (if not slow) stage of the project.
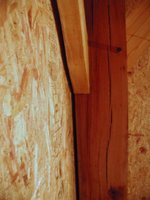
There is a fairly standard trick to hanging drywall in a timber frame house: When you install the SIPs, you hold them away from the timbers using 5/8" strips of wood or plywood. This gives you ample room later to slide a piece of 1/2" dry wall behind the timbers and knee braces. As the timbers and braces shrink, they simply expose more of the drywall. The alternative would be to fasten the SIPs directly against the timbers, but then you would have to butt your drywall up to the timbers and cut drywall to fit around the braces - not desirable, especially since these timbers are still shrinking! Here's a picture that illustrates the intentional gap we left between the SIPs and timbers.
4 Comments:
Your living our dream!! Very impressive work! I just found your blog, and have already learned a great deal. We are retiring to a farm in East Tennessee in a few weeks and want to do what you have done...build our own Timber Frame (you sold me on the Grand Oaks Timber Framing Workshop). We purchased a Woodmizer, have plenty timber on the farm and I had a few questions. You mention that you used around 12 species of wood in the frame. Would you do this if you could only choose one? In other words, have you had any trouble or does it look odd? It looks like you were able to use oak in most if not all the bents and the other woods in the sills, etc., but you mention you liked working with poplar. Are any of your timbers over 20 ft long (the Woodmizer only cuts a 20 ft log unless you get the extension). Did you get your locust pegs from Northcott Wood Turning? It appears you have a Makita 16 5/16" Beam Saw, the 7104L Chain Mortiser and the 12 1/4 inch Power Planer. Other than chisels and mallets, any other special tools (housing router)? What CAD program did you use? You used standing seam under the solar panels...who did you go with? Why not geothermal for heating/cooling (maybe I missed it)? What exterior to you plan on using? We were thinking of stacked stone (a lot of sandstone on our place also), poplar bark siding, and batten and board. Lots more to ask...keep the blog going.
Your living our dream!! Very impressive work! I just found your blog, and have already learned a great deal. We are retiring to a farm in East Tennessee in a few weeks and want to do what you have done...build our own Timber Frame (you sold me on the Grand Oaks Timber Framing Workshop). We purchased a Woodmizer, have plenty timber on the farm and I had a few questions. You mention that you used around 12 species of wood in the frame. Would you do this if you could only choose one? In other words, have you had any trouble or does it look odd? It looks like you were able to use oak in most if not all the bents and the other woods in the sills, etc., but you mention you liked working with poplar. Are any of your timbers over 20 ft long (the Woodmizer only cuts a 20 ft log unless you get the extension). Did you get your locust pegs from Northcott Wood Turning? It appears you have a Makita 16 5/16" Beam Saw, the 7104L Chain Mortiser and the 12 1/4 inch Power Planer. Other than chisels and mallets, any other special tools (housing router)? What CAD program did you use? You used standing seam under the solar panels...who did you go with? Why not geothermal for heating/cooling (maybe I missed it)? What exterior to you plan on using? We were thinking of stacked stone (a lot of sandstone on our place also), poplar bark siding, and batten and board. Lots more to ask...keep the blog going.
Rick,
Grand Oaks - definitely step #1 if you are in Tennessee.
Woodmizer - it will do everything you need and more. 8 sided timbers, 5 sided timbers - your imagination and free time are the only real limits to this machine. I cut some of my timbers to 26+ feet on my 20.5' bed without buying the bed extension. It's a bit of a pain, but if you have less than a dozen long timbers to cut, save your money and do what I did. Cut the first 20 feet of the timber and let 4 to 6 feet of log hang off of the bed (block it up out there if you're hanging more than 3' over the end). Then slide the log onto the bed and finish cutting the timber.
If I had to chose only one wood for timbers it would be white oak. Extremely durable and a good choice for a DIY project, since you can leave the timbers in the open for long periods of time without worrying too much about rot. Since most commercial frames are built from softwoods (pine for instance), don't let anyone tell you that your hardwoods, whatever the species, are not suitable for timber framing. There seems to be a lot of misinformed arrogance out there regarding wood selection. (look in the "wood properties charts" available on line to pick your hardwoods - or better yet, get Sobon's books)
Locust pegs - I cut 1" boards out of 5" to 6" locust logs that I had harvested (from grown over fields) and had intended to use for fence posts. My brother-in-law ripped them into octagon shaped pegs on a table saw. Black locust pegs are twice as good as white oak pegs. Make them longer than you think you'll need - 16" is a good length.
CAD program - I used AutoCAD LT. Definitely "taking the short bus to school." For a convoluted frame like mine, it would have been worth the time to learn a 3D package. For a less complicated frame, you might get by with only hand sketches. I know I spent over 1,000 hours in the CAD package. 3D capability would have made cross checking (which takes longer than drawing!) the joints much easier. If you can find premade (and guaranteed!) plans that suit your tastes, you would be way ahead of the game to buy plans.
Geothermal (actually run to our pond) is definitely in the plans - at least for air conditioning.
Buy the special tools (none are necessary) in this order depending on your finances:
1. chain mortiser and an extra chain so you always have a chain while the other is being sharpened. This single tool alone will cut your workload in half.
2. Makita pizza saw. (we call it a pizza saw because the blade is the size of a pizza) I got 1/3 of the way through my project before I decided to buy this saw. It is the cheapest and least specialized of the speciality tools. Not a must have, but a very nice to have. Good bang for the buck. Seriously consider a left handed 8" wormdrive saw too. When you start cutting dovetail pockets, you will understand why a left handed saw is handy.
3. Planer. Debatable whether you need this. My wife wanted planed timbers, so I needed this tool. It's a non-trivial amount of extra work to plane your timbers and be ready to buy lots of blades at something like $30 a whack. Great tool but will cause you more work, not less work. Overpriced for what it is. Not something you would call "Bang for the buck." I would buy it again though. I used it to plane all of my timbers to exact dimensions thereby making layout easier for me (and the non-timberframe learn-ed people that helped me).
4. I still do not own a router. We are using my bro-in-law's router to do the radiant tubing grooves right now. Never used it on the frame. Scott (the timberframe instructor) and I got into a friendly race on identical housed mortises while he was here helping me. He used a router, and I did not. The result was a toss-up. (I think I beat him, but I was sweating a lot harder and he would have probably beat me on the second housed joint if we continued that pace).
OK, well, there are the answer's to most of your questions. Remember, free advice is usually worth what you pay for it, and opinions are like buttholes (everyone's got one and they all stink), so take all of this with a grain of salt. :)
You are welcome to visit here when you get seriously close to starting your timberframe, but you're probably pretty serious if you already have a woodmizer and a wood lot. At some point, I would also consider helping other DIY's if it would help finance the finishing of my own house. Got anything to trade? :)
Thanks for the quick info...free advice from the school of hard knocks is always worth the price d:) We are going to start a pick your own operation to try and make ends meet along with 25 or 30 head of Angus. First off will be two acres in blueberries and Muscadines. We have 70 muscadine vines in and plan on putting 300 blueberry plants in the end of April. Grew up on a farm and it has taken me 30 years to save enough to move back.... Your wife sounds like mine...29 years and hoping for 29 more! The old farm we bought has bee logged several time. Best timber on the place is hard maple and hickory, but lots of poplar and some gorgeous old short leaf pine. We would love to come visit and talk trade. I retire the end of April and then my time will be mine!
Post a Comment
<< Home